
SOMS
The technology
The Smart Optical Monitoring System (SOMS), when installed on a welding robot, observes in real time the plasma generated during a welding or material deposition operation. By performing a multi-spectrum analysis, it identifies and categorizes different types of defects, and then essentially “teaches” the host welding equipment to avoid those defects and create better welds or material depositions with the desired composition and phase transformation.
Closed Loop Control System
We offer a robust closed control system designed for the customer to adjust the welding parameters based on the SOMS prediction of the weld quality.
SOMS for blood and skin disease test:
A Smart Optical Monitoring System (SOMS) to monitor blood or skin disease is under development. The sensor will be able to detect blood glucose level or skin cancer without drawing blood .
Special Features of SenSigma’s Product SOMS
• Compact size, light weight
• Reasonable price
• Easy implementation and low operating cost
• Suitable for both laser and plasma metal processes
• Fast signal processing capability
• Insensitive to ambient disturbance
• Capable of co-axis operation with laser welding application
• Capable of integrating into NC machine or feeding signal back to NC machine for process control
Optical Emission Spectroscopy
The spectroscopic sensor will predict composition, phase transformation and manufacturing defect and will allow for the fabrication of near net shape ad property (NNP)
Welding Quality Monitoring
By monitoring the temporal zinc spectral line and signal strengths, SOMS can predict the gap effect of lap joining of galvanized steel plates. By monitoring multiple information such as line intensity, standard deviation, plasma temperature or electron density, and by using different signal processing algorithm such as vector machine training or wavelet transforming, weld defects can be detected and classified.
Microstructure and Composition Prediction
Through analyzing the line intensity ratio of different elements during laser/plasma metal manufacturing process, SOMS can predict both composition and phase transformation based on a pre-established calibration curve. In the Ni-Ti binary direct metal deposition process, a change of the line intensity slope represent a phase change; while within a same slope, elemental composition can be predicted.
LEARN MORE ABOUT SMART OPTICAL MONITORING SYSTEMS
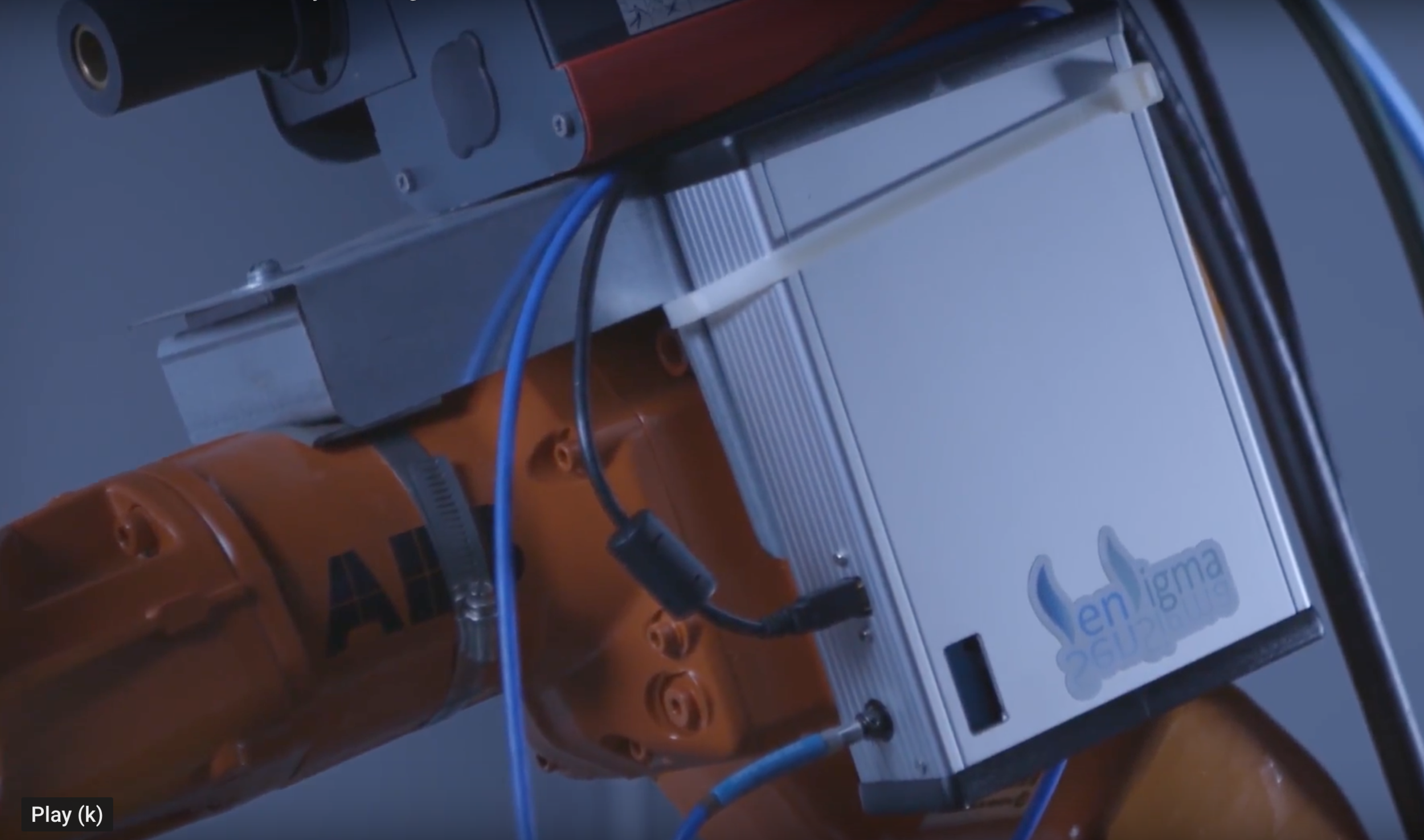